Climate change, sustainability and energy efficiency have never been so high on the political agenda. The UN’s recent Climate Change Conference (COP26) in Glasgow, UK brought the world’s political leaders, Non-Governmental Organisations (NGOs), businesses and scientists together with the aim of accelerating action towards the goals of the Paris Agreement on Climate Change. The question for those of us at the industrial machinery level, is how can we contribute? Today, I see a new generation of engineers keen on influencing the industrial world in a positive way, creating machines that attain new levels of energy efficiency to help protect the Earth for future generations.
By Séamus Dunne, Actuator Section Technical Manager, SMC European Technical Centre
JANUARY 2022
By designing industrial machinery and systems for an operating pressure of 4 bar, rather than 7 bar, end users can cut their energy consumption by up to 29%. With such an enormous environmental benefit on offer, the question is how to turn this idea into reality? SMC’s Industry Projects Manager for Europe, Andy Still, has extensive experience in this area. Check out his article on energy efficiency: ‘Release the pressure’.
Here at SMC, thinking about our energy-saving products, we offer both ISO and non-ISO cylinders; each has its own attributes and advantages. ISO cylinders prove beneficial in a variety of different applications which, in addition to their consistency in dimensions (regardless of pneumatic supplier), is why they remain popular for industrial machinery projects around the world. However, if you really want to push energy efficiency to new levels, I’d suggest that non-ISO solutions are the product of choice.
Our engineers in Japan are always looking to design more efficient alternatives in order to drive down energy consumption and help OEMs create more sustainable solutions. We believe that more compact and lighter is the way forward for those seeking ultra-efficient solutions. Less material means lighter machines and lower shipping costs. Smaller products ultimately lead to smaller machine footprints. More machine lines can be installed into factories increasing productivity. And, although I can’t state that lighter and smaller always translates into less air consumption, fitting such components to moving parts of the machine can translate into less energy consumption.
To give you an idea of the difference between ISO and non-ISO, here’s one example: compared with the SMC C96-C ISO cylinder (50 mm bore, 100 mm stroke), the length of our new JMB series demonstrates an 18% length reduction, while width is 9% less and weight is 39% lighter. Notably, it is possible to deliver air consumption savings through the use of intermediate bore sizes. For instance, to move a workpiece with a weight of 37 kg, a cylinder with a bore diameter of 43 mm or more is required (if operating at 5 bar pressure). Previously, a conventional 50 mm diameter bore would have been the closest option since the next smallest size, 40 mm, has insufficient output. However, with the newly released JMB cylinder in 45 mm diameter bore, sufficient output is available while also saving air due to a 0.4 L (ANR) reduction in air consumption compared with the 50 mm variant.
SMC´s JMB Series – Offers intermediate bores
Customers frequently tell me they want more compact cylinders that still offer optimal performance while also reducing energy requirements. Unfortunately, achieving these optimisations and the high levels of energy consumption savings that the climate crisis demands, is extremely difficult within the constraints of ISO 15552. Although we of course continue supporting customers with an extensive range of ISO cylinders and options, we’re advancing the development of other cylinder ranges - such as our JMB series - to satisfy market demand for more compact and energy-efficient products. We are at a time of critical decision-making for the entire planet. Let’s make the right choices.
Additional graphical data
Air consumption can be reduced by optimal size selection
EXAMPLE
In order to move a workpiece with a weight of 37 kg, a bore size of Ø 43 or more is required. Previously, a Ø 50 bore size would have been the closest option since the next smallest size, the Ø 40, has insufficient output. However, with the newly released bore size of Ø 45, sufficient output can be obtained while also saving air due to a 0.4 L (ANR) reduction in air consumption compared with the Ø 50.
∗ Conditions/Supply pressure: 0.5 MPa, Load factor: 50 %
Current bore size output
NOTE 1 - Supply pressure: 0.5 MPa, Load factor: 50 %
When the intermediary bore size of Ø 45 is used
NOTE 1 - Supply pressure: 0.5 MPa, Load factor: 50 %
AIR CONSUMPTION - Ø 50: 2.2 L (ANR) − Ø 45: 1.8 L (ANR) = 0.4 L (ANR) 18 % reduction
Air cylinder and ISO 15552 Cylinder dimension & weight comparison
Compared at ø63-200 mm stroke
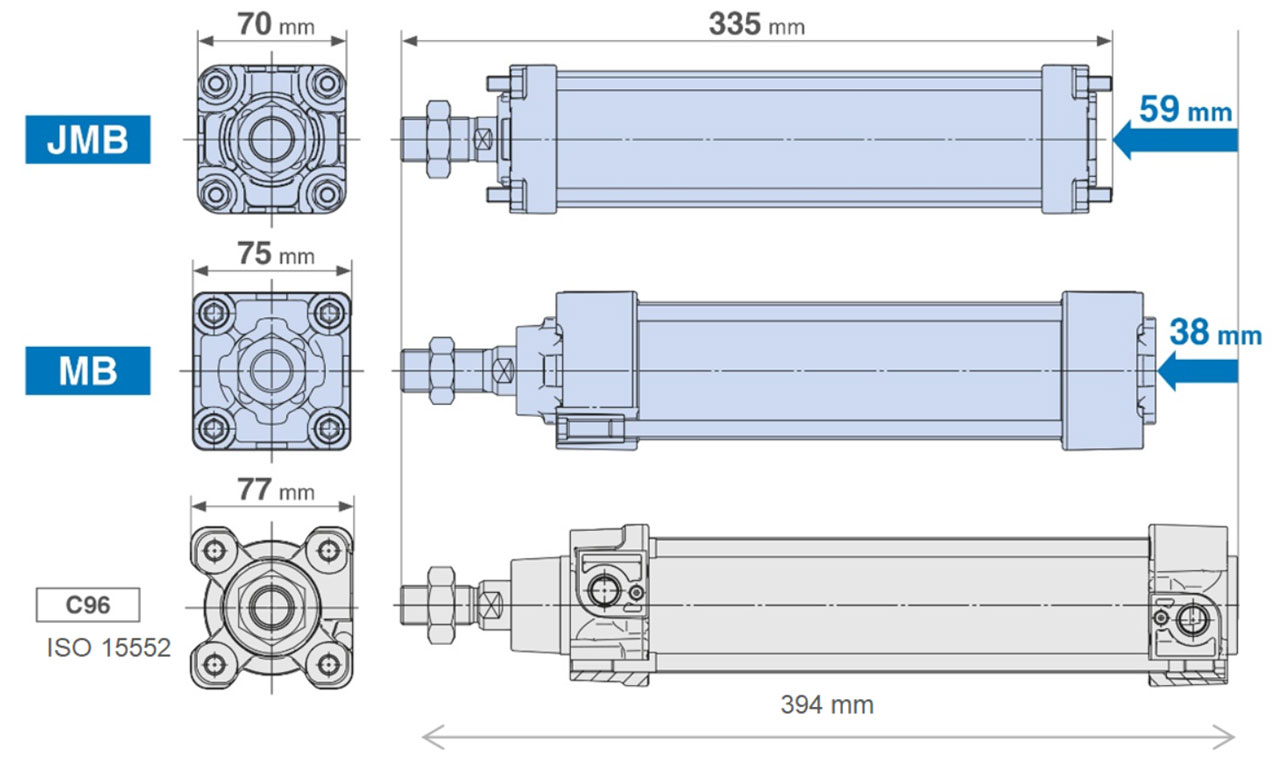
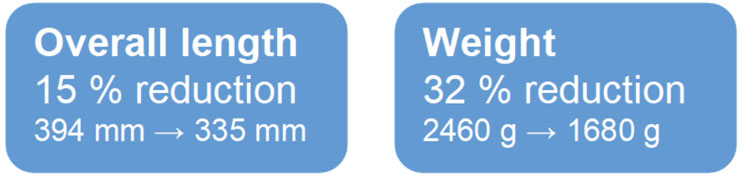
For CO2 emissions reductions of our ISO cylinders versus their Non ISO alternatives, please check the Sustainable Management of CO2 catalogue here.