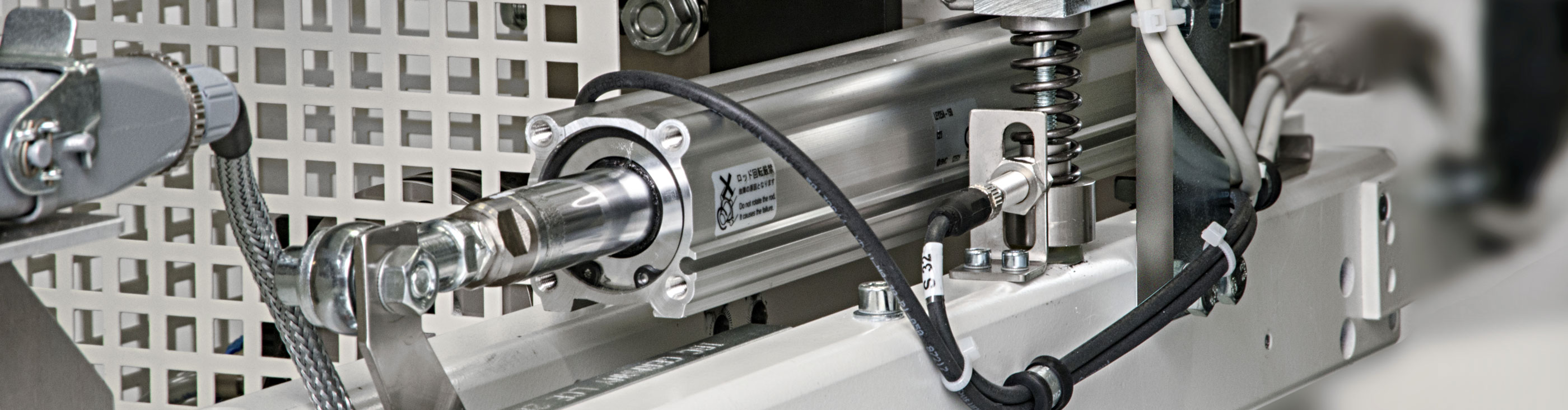
While large companies are focusing entirely on digitisation, many small and medium-sized businesses are dependent on person-to-person support. Instead of investing energy in developing digital platforms, the innovativeness in this segment primarily arises from integrating external expertise into the development process. And this happens in an entirely hands-on, face-to-face manner, rather than virtually. The great success of this method indicates that it won't be going out of style in a hurry.
By Alexander Schur, Sales Engineer SMC Germany
For almost 60 years, Beck Packautomaten GmbH & Co KG in Frickenhausen, Swabia, has been developing and manufacturing film and shrink packaging systems for more than 40 industries. The company has developed packaging machines that produce specially adapted shipping bags for mail-order retail. The format of the shipping bags automatically adapts to the packaged products. The bags are labelled during the packaging process, perforated to enable rapid opening and return, and given a carrying handle. This is especially practical if customers pick up their parcel that they ordered online from a shop and carry it home; it also allows the parcel service to hang the delivery on a door. Since the handle must always be centred on the different sizes of shipping bags, a sealing element moves into the exact position for each packaging unit to punch the handle. This task must be performed with high speed, precision and reliability.
To make adjustments for the handle, Beck Packautomaten used an electric cylinder with a stepper motor. However, this pair proved to be a weak point in the machinery concept; it was too weak, too vulnerable and, at the same time, somewhat cumbersome with regard to communication and configuration. Beck Packautomaten turned to SMC – one of the world's leading suppliers of individual automation solutions – in search of a replacement. The requirements for the new product combination are almost typical of the current situation in mechanical engineering: a compact design due to little available space, simple connection to the existing Siemens control system by means of PROFINET®, as well as – it almost goes without saying – high reliability combined with the lowest possible costs. The physical specifications demanded a minimum adjustment track of 150 mm and a maximum adjustment time of one second.
Integration via plug & play
"We received the best advice even when designing the system," says Mark Hübsch-Dolde, Head of Electrical Construction at Beck Packautomaten, summing up his initial impressions. SMC chose the stepper motor controller JXCP1 and the LEY25A drive for this application. The controller communicates directly and openly in PROFINET® networks at high speed in real time. Thanks to its dual-port IN/OUT connection, the controller offers great flexibility and supports both a Device Level Ring (DLR) topology and line topologies. The parameterisation is very easy and can be carried out via user-friendly Windows software; operation via a handheld terminal is also possible as an alternative. The drives are directly controlled; additional gateways are not required. The stepper motor controller JXCP1 is compatible with almost all stepper motors of SMC's LEY series, meaning that it is possible to integrate it via plug & play.
Intelligent peripherals
Unipolar stepper motors provide the electric drive of the LEY series. An encoder is installed as standard, meaning that operation is controlled in a similar manner to a servo drive. The drives can run to a defined force and report back the current actual position when this value is reached. All LEY series drives are equipped with a piston rod and can execute strokes from 30 to 150 mm. Depending on the model, repeat accuracy of up to ± 0.02 mm is achieved. The thrust energy can reach up to 141 N; speeds of up to 350 mm/s are possible in thrust operation.
The shell and seals of the cylinder durably and securely protect the electric motor and piston rod inside from dirt. This makes the drives of the LEY series extremely durable in practice. At the same time, they can be easily mounted in the immediate vicinity of the application, even if they are exposed to high levels of moisture or dust.
Convincing demonstration
The project managers from Beck Packautomaten could see for themselves just how easy it is to connect the controller/stepper motor assembly to the packaging machine. "Everyone was delighted with the simple configuration and commissioning," recalls Mark Hübsch-Dolde. Integrating the new products went without a hitch for the machine manufacturer, thanks to the free support during the initial commissioning.
Manufacturer profits from huge benefits
Overall, this cooperation benefits the machine manufacturer in many ways: the controller's simple configuration halves commissioning times and the integrated PROFINET® interface allows connection to the existing machine concept without additional hardware. At the same time, JXCP controllers also offer the opportunity to control different units with only one device. This opens up the possibility of operating other drives with the controller. Based on its positive experience and the thoroughly professional support, Beck Packautomaten now wants to put other pneumatic components to the test. It is therefore possible that we will be seeing further improvements soon. And all in a very traditional way, via a face-to-face skills network instead of the oft-invoked digital version.