The subject is more than serious. Pneumatic equipment accounts for about 20% of all factory power consumption and there is a proven way to improve energy efficiency: reduce the operating pressure. SMC explains how companies can achieve this objective and thus fall in line with manufacturing’s most important current trend.
By Andy Still, Industry Projects Manager, Energy, Europe
MARCH 2021
For most industrial plants, typical operating pressure (or main compressed airline) is between 6 and 7 bar. However, by simply lowering the pressure to 5 bar, facilities can reduce their energy consumption up to 15%, while dropping the pressure to 4 bar offers savings of up to 29%.
The global understanding of pressure reduction is that it will affect performance. Although this statement is true for some equipment, it must be said that most workstations will keep running normally.
Industrial companies cannot afford loss of performance or time stop in their operation, so they need a safe and reliable way of reducing pressure. With this thought in mind, at SMC we have devised a solution based on comprehensive system analysis at the outset of the project. The objective is to make sure that first the available power is utilized in an optimized way and second to smooth the demand peaks.
Identification of the main problems
In just a few days, without interrupting operation, an audit is carried out. There are many facets to this analysis. A first step is to evaluate the compressor operation and address the filtration components to ensure the system will not exhibit any pressure drops and deliver consistent flow across the entire pneumatic circuit.
SMC determines air quality by carrying out a dew point analysis and collecting a particulate sample of the compressed air. Then, we also undertake ultrasonic leak detection; tagging, photographing and cataloguing each leak, with a short ROI if repaired. Finally, our experts investigate any equipment exhibiting increased air demand, and identify compressed air inefficiencies and energy costs.
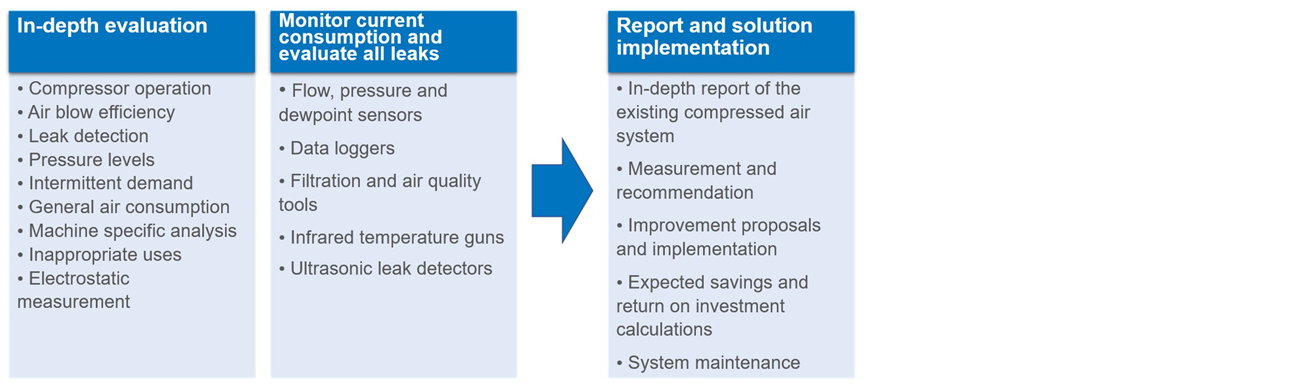
These initiatives help to determine existing conditions and minimum pressure requirements for the plant’s compressed air system. SMC can then provide recommendations/solutions, including the estimated costs to eliminate inefficiencies and assure system reliability when reducing the pressure. Industrial companies can lower the operating pressure without fixing every issue. The order of priority must be the elimination of leaks, the smoothing of pressure peaks and finally the improvement of the energy efficiency of each of the components.
Permanent leak elimination
Today, some plants suffer from 20 to 50% leakage rates due to poorly maintained compressed air systems. We identify all leaks and fix them accordingly, by correcting seals or tubing for instance. But this action only offers a temporary improvement. Further leaks will inevitably occur and small leaks will eventually become larger ones. There needs to be a policy in place that assures leak repair as an ongoing, continuous project. A leak detection system is highly recommended as it avoids future leakage costs and wasted energy.
Smooth demand peaks by upgrading the components which consume the most and optimizing the regulation
As part of SMC’s role to identify any equipment that generates high demand, the primary consideration should be air blow systems as these account for 42% of global consumption and offer the potential to compromise entire system continuity. To help counter this issue, we can provide a solution that reduces air consumption up to 85%, generating shorter but higher impact-pressure peaks.
A second option is to replace the air blow system with a mechanical alternative, if possible. This choice involves a small investment, but the return is fast due to the high consumption of air blow equipment. It is also important to consider vacuum systems, which represent 9% of global consumption. Here, a vacuum unit featuring SMC’s energy-saving digital pressure switch enables plants to reduce air usage by 93%.
Smart regulation with appropriate valve technology also serve to balance the circuit, reduce peaks and allow the use of lower pressure when possible. For instance, actuator return strokes can often function with a lower operating pressure, sometimes 2 bar or less.
A step beyond: eliminate all inefficient components to achieve 75% less energy consumption
Achieving the previous steps, almost all industrial plants should be able to reduce operating pressure without any risk. A next step, and not such a complicated one, will be to optimize any single machine components. Small improvements in cylinder performance generate big gains. As a result, our experts consider the stroke, the fittings, the mounting and certain other adjustments to achieve optimum performance with the lowest energy consumption. We specify the best actuator for the application, including cylinders sized exactly to the load.
It is of the first importance to ensure that all components have the correct sizing, which is where SMC can offer expert advice. Our company is the only supplier on the market providing intermediate size options in order to deliver best-fit solutions for every application.
Further advice will include the potential adoption of low-energy consumption components, such as air-saving circuits, pressure reducing components, or switch-off power. The installation of a digital gap checker in machining applications (for workpiece placement confirmation) can also make a notable difference as it provides a 60% reduction in air consumption. This detection principle ensures a flow rate of 0 L/min when the workpiece is seated in its fixture.
The combination of reduced operating pressure and system improvements brings huge savings in energy consumption, usually around 75%.
SMC has a dedicated Energy Efficiency team which provides differentiation via its constant presence on the factory floor, from where it offers customer assistance from the initial analysis phase, to final implementation. Our skilled teams have accumulated the necessary knowledge and experience to lower system pressure without risk.
Industrial companies should move now to reduce their carbon footprint and achieve significant savings.