With energy prices surging across Europe, efficiency has become a high priority for all manufacturing and process plants using vacuum handling systems. Fortunately, based on decades of experience and know-how, SMC can outline four simple ways that you can reduce the energy consumption of your vacuum system. Using less energy per lift/transfer will provide a direct contribution to your bottom-line profitability while simultaneously supporting industry’s drive to net-zero carbon emissions.
By Martina Höller, Electrical technology product manager CEE, SMC Austria
JUNE 2022
The latest energy-saving technology and process engineering can make a genuine difference to vacuum handling applications, whether the sector is packaging, metalworking, automotive, healthcare or any other. Simply follow these four steps to see a notable improvement in your system’s efficiency.
It’s possible to generate vacuum centrally by means of a vacuum pump or de-centrally (directly on the machine) using vacuum ejectors. SMC’s extensive range of vacuum ejectors – from super compact inline ejectors up to ultra-high efficiency multi-stage ejectors with high-performance silencers – are suitable for vacuum flows up to 600 Nl/min, thus meeting the needs of almost any industrial application.
Every type of ejector has its specific parameters, which are dependent on one another. These include: standard supply pressure (the amount of compressed air you need to achieve the highest possible vacuum pressure); maximum suction flow rate (volume of air taken in by the ejector); maximum vacuum pressure (maximum value of the vacuum pressure generated by the ejector); and air consumption (the amount of air consumed by the ejector when operating with the standard supply pressure).
4 bar: the optimal supply pressure (on average) for SMC ejectors
Ask yourself, do you really need the maximum vacuum pressure to handle your workpiece? You need to pose this question because the level of vacuum pressure will relate directly to your air consumption and your costs. By way of example, if you use of 0.5 MPa (5 bar) main line supply pressure to operate our ZL112A ejector (with valves), your air consumption will total around 78 l/min (4680 l/hour) to achieve a maximum vacuum pressure of -84 kPa. However, by choosing to operate the ejector at a reduced 0.35 MPa (the standard supply pressure for this type of ejector), you can cut air consumption to 57 l/min (3420 l/hour) and still achieve the same maximum vacuum pressure (-84 kPa). A significant 27% energy saving.
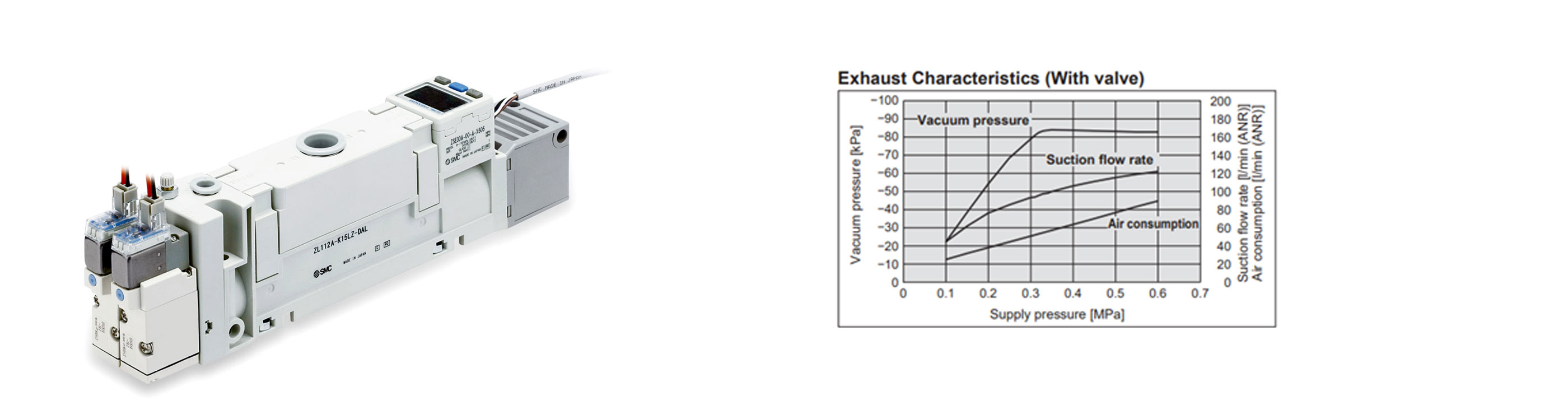
SMC´s Multistage Ejector – ZL Series A light efficient push to your suction
Picture on the right: Extract from ZL´s catalogue
As a point of note, while many manufacturers have yet to transition from 7 bar standard shop pressure, optimal vacuum operation takes place at an average of 4 bar, so reducing from 7 bar to 4 bar not only benefits your bottom line and the future of the planet, it will have no impact on the effectiveness of your operations.
Returning to the example, if you can safely handle the workpiece with a maximum vacuum pressure of -65 kPa, you can reduce the supply pressure even further, to 0.25 MPa (2.5 bar). This would cut your air consumption to 45 l/min (2700 l/hour), delivering an impressive 43% energy saving.
Use a bigger pad diameter, not higher supply pressure
Some engineers make the mistake of increasing supply pressure to achieve a higher holding force, but this leads to more energy consumption and more cost. In fact, it’s directly proportional, so doubling the vacuum pressure will double your holding force and double your energy costs.
Instead, it may be possible to increase the diameter of your vacuum pads in certain applications. When doubling pad diameter, your holding force quadruples, while your energy costs remain the same as there is no increase in supply pressure. The price difference between a 20 mm and 40 mm diameter vacuum pad is typically less than €5.
Vacuum ejectors with energy-saving function
Some vacuum ejectors feature a vacuum pressure switch with an energy-saving function that can reduce energy consumption by up to 93%. So how do they work? Well, you first define the pressure range within which you can securely hold the workpiece, for example from -65 to -55 kPa. The integration of pressure switch with energy-saving function serves to cut off the air supply upon reaching the desired vacuum level. Vacuum only generates again when the pressure falls below the lower range, in this case -55 kPa.
SMC´s Vacuum Unit – ZK2-A Series: The all-in-one silent energy saving solution
Take a vacuum handling application involving a conventional ejector that operates at 450 cycles per hour, 10 hours a day, for 250 days a year. Such a system will consume around 9350 m3 of compressed air every year. However, using a vacuum ejector with an energy-saving function will reduce air consumption to just 638 m3 per year, delivering the aforementioned 93% saving. The potential savings are higher in long-cycle applications.
Smart management
To maximise the use of an energy-efficient vacuum handling system, SMC recommends that you adopt ‘smart’ ejector systems. A serial transmitted ejector manifold requires no separate input/output units to operate and avoids complex electrical wiring of the valves and sensors.
Field devices can connect directly to the PLC. Via the PLC, it is possible to set and monitor the pressure values, suction or release verification, the energy-saving function and the valve protection function. This concept leads to better control of your application, more valuable data, simple set-up and on-board product diagnostics, as well as easy monitoring.
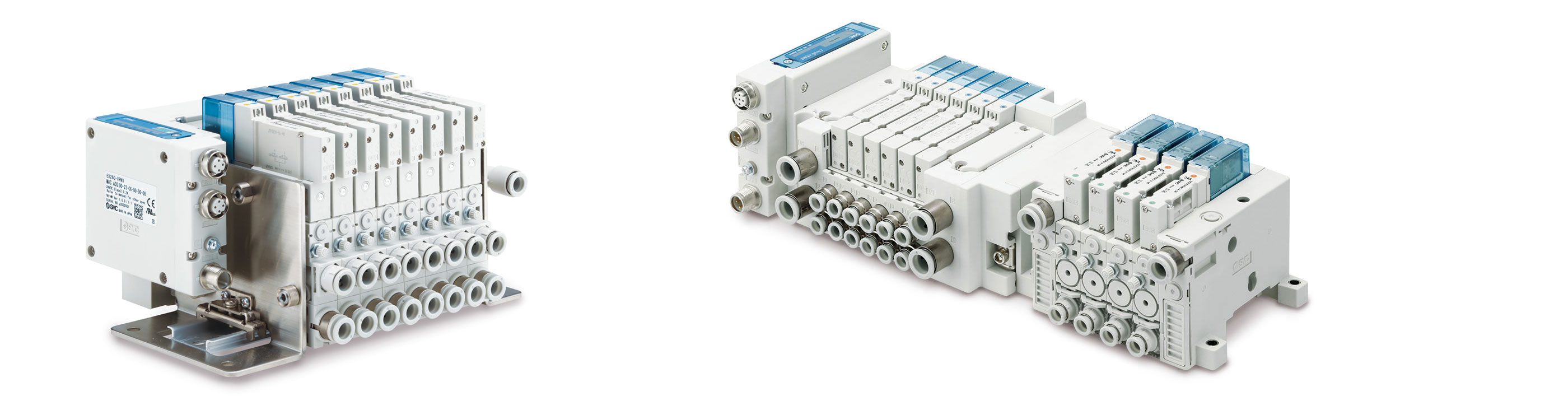
SMC´s Valve and Ejector Combination Manifold – JSY Series Combinedly control your Valves & Ejectors
Product on the right: SMC´s Vacuum Manifold for Fieldbus – ZKJ Series Control your vacuum remotely & efficiently
Technical support
If you’ve ever dealt with a vacuum-based system you’ll be aware that vacuum can be unpredictable as the interaction and the behaviour between workpiece and pad differs depending on the application. The only real way to be certain of the results is to take advantage of an expert technology supplier such as SMC, which can conduct tests at customer sites or at its laboratories located across Europe. Vacuum is frequently about trial and error regarding pressure, flow, pad size, number of pads and more, particularly if it involves special workpiece materials, so why not let the experts work it out.
With energy costs rising rapidly around the globe, few can afford to ignore the energy-saving possibilities that a correctly specified and configured vacuum handling system can bring. It’s time to get a grip on efficiency.