Energiahatékonyság növelés a sűrített levegős rendszerekben
A gyárakban járva gyakran találkozunk azzal a jelenséggel, hogy a dolgozók a sűrített levegős tömlőket kilyukasztva hűtik magukat, mondván „a levegő ingyen van”. Ez természetesen a sűrített levegő esetében nagyon nem igaz. Az ipar a teljes energiafelhasználásának 20%-át a sűrített levegő előállítására fordítja. A befektetett energiának azonban csak mintegy 20%-a az, amiből ténylegesen sűrített levegőt állítunk elő, a többi veszteség. Mindezen számok tükrében érthető, miért kiemelten fontosak az energiahatékonyság növelésének szempontjából a sűrített levegős rendszerek.
Korunk egyik legfontosabb feladata a rendelkezésünkre álló energiahordozók minél hatékonyabb felhasználása. A fenntartható jövő, a CO2 kibocsátás csökkentése mellett a gyáraknak ez kiemelt érdekük a versenyképességük javítása, és a költségeik csökkentése miatt is. Amennyiben a cégek az ISO 50000:1 tanúsítvánnyal szeretnék a saját márkájuk értékét erősíteni, szintén elengedhetetlen a folyamatos fejlesztés, a hatékonyság folyamatos növelése.
Mit tehetünk? Sűrített levegő használata esetében talán a legfontosabb, hogy belássuk, igazán komoly eredményeket csak úgy érhetünk el, ha rendszerben gondolkozunk és folyamatosan törekszünk jobb megoldásokat találni. Nem elég egy-két dolgon javítani és utána hátra dőlni.
Első lépés legyen mindenképp az, hogy csak annyi levegőt és olyan nyomáson állítsunk elő, amennyi ténylegesen szükséges a gyártási folyamatokhoz. Munkánk során sokszor tapasztaljuk, hogy a kompresszorok 8-8,5 bar nyomást állítanak elő, holott az egész gyárban alig néhány gép igényli ezt, az összes többinek elég lenne a 6-6,5 bar. Mit tegyünk? Fel kell mérni a gyárban, melyik gépeknél szükséges a magasabb nyomásérték. Ha ez megvan, készíteni kell egy megtérülési számítást, hogy megéri-e ezek elé nyomásfokozókat beépíteni (amelyek külső segédenergia nélkül a betáplált nyomást 2 vagy akár 4-szeresére növelik). Ezt követően meg kell vizsgálni, hogy a kompresszorok által előállított hálózati nyomás milyen mértékben csökkenthető. Általában igaz, hogy 1 bar nyomáscsökkentés kb. 10%-os energiamegtakarítást jelent. Ez a közvetlen megtakarítás, emellett számolhatunk még a szivárgásból adódó veszteségek csökkenésével, a kompresszor karbantartási költségeinek csökkenésével, az élettartalmának növekedésével. Tapasztalataink alapján a felülvizsgálatot követően nem egy esetben egy kompresszorral kevesebb is elegendő lett az üzem sűrített levegői gényének kiszolgálásához.
Felmérések szerint a sűrített levegős rendszerek energiahatékonyságának növelésében a legnagyobb potenciál a hővisszanyerésben van. Így fontos, hogy miután már csak a szükséges mennyiségű levegőt állítjuk elő, a fennmaradó hőveszteségekből minél többet visszanyerjünk, és fordítsuk azt akár a csarnokok fűtésére, akár használati melegvíz előállítására.
A következő elengedhetetlen lépés, hogy mérjük, monitorozzuk, mennyi a tényleges levegőfelhasználás, hiszen mint tudjuk, amit nem mérünk, azt nem is tudjuk fejleszteni. Azon túl, hogy fontos tudnunk mennyi levegőt használunk fel a gyártási folyamatokhoz, a monitoring rendszerekkel a veszteségeinket is pontosabban megismerjük, és megkönnyítjük azok feltárását.
A fent említett felmérések szerint a 3. legnagyobb potenciál a sűrített levegős rendszerek energiahatékonyságának növeléséhez a szivárgások megszüntetésében van. Egy 5 évnél idősebb rendszerben 25% vagy afeletti lehet a veszteség szivárgások formájában.

(6 bar; 5 Ft/m3; 8740 óra/év)
Ezek megelőzésében, feltárásában segíthetnek az SMC automatikus szivárgás detektáló rendszerei. Ha ilyen nincs a gépekbe beépítve, akkor pedig a szivárgás kereső szolgáltatásunkkal tudunk segíteni. Éves szinten kollégáimmal több 100 millió forintnyi szivárgási veszteséget tárunk fel és nyújtunk át jegyzőkönyvben egyéb javaslatainkkal együtt ügyfeleinknek. De önmagában ez még nem megoldás, hiszen emellé kell még a partnerünk részéről a törekvés, hogy ezeket megszüntesse. Amennyiben megvan az együttműködés, tapasztalatok szerint már néhány alkalom után, akár negyedére is csökkenthető a feltárt szivárgások száma (apró adalék: a feltárt szivárgások 60-70%-a a csatlakozásoknál keletkezik, amik minimális költséggel és időigénnyel javíthatók).
Ezzel párhuzamosan meg kell vizsgálnunk, az energiahatékonyság növelő termékek alkalmazásának lehetőségét. Mikre gondolunk? A teljesség igénye nélkül, pusztán gondolatébresztőnek álljon itt néhány példa:
- Vákuum ejektoraink nyomásérzékelővel és visszacsapó szeleppel felszereltek, így csak akkor használnak levegőt, amikor tartják a munkadarabot és a vákuum egy megadott érték alá csökken.
- Hűtéshez, szárításhoz használt fúvókáink harmadára, negyedére csökkentik a felhasznált sűrített levegőt. A többit kialakításuknak köszönhetően a környezeti levegőből használják fel.
- Nyomásszabályzóink segítségével csak a szükséges és optimális nyomásértékű levegőt juttatjuk az ejektorokhoz, munkahengerekhez.
- Mágneses megfogóinkkal nem használunk sűrített levegőt, ahol nem szükséges.
- Többlépcsős ejektoraink többszörösére növelik a vákuumtechnológia hatásfokát.
- Hűtveszárítóinkkal biztosíthatja a megfelelő levegőminőséget, így csökkentve a legyártott selejt termékek számát.
Azonban mielőtt bármilyen terméket beépítünk vagy kicserélünk, fontos a dolgozók tájékoztatása, motiválása. Egy 1 mm-es lyukon, 6 bar-on, 3 műszakkal számolva éves szinten 200.000 forintnyi sűrített levegő szivárog el! Tudatosítani kell mindenkiben, hogy a sűrített levegő nincs ingyen! Ha egy gép az adott műszakban, vagy egy egész hétvégén nem termel, ne csak áramtalanítsuk, hanem kapcsoljuk le a levegőt! Annál nagyobb pazarlás nincs, amikor úgy keletkezik veszteségünk, hogy közben nem is termelünk.
Kérdésekkel, tanácsokért, közös megoldásokért keresse bátran kollégáinkat.
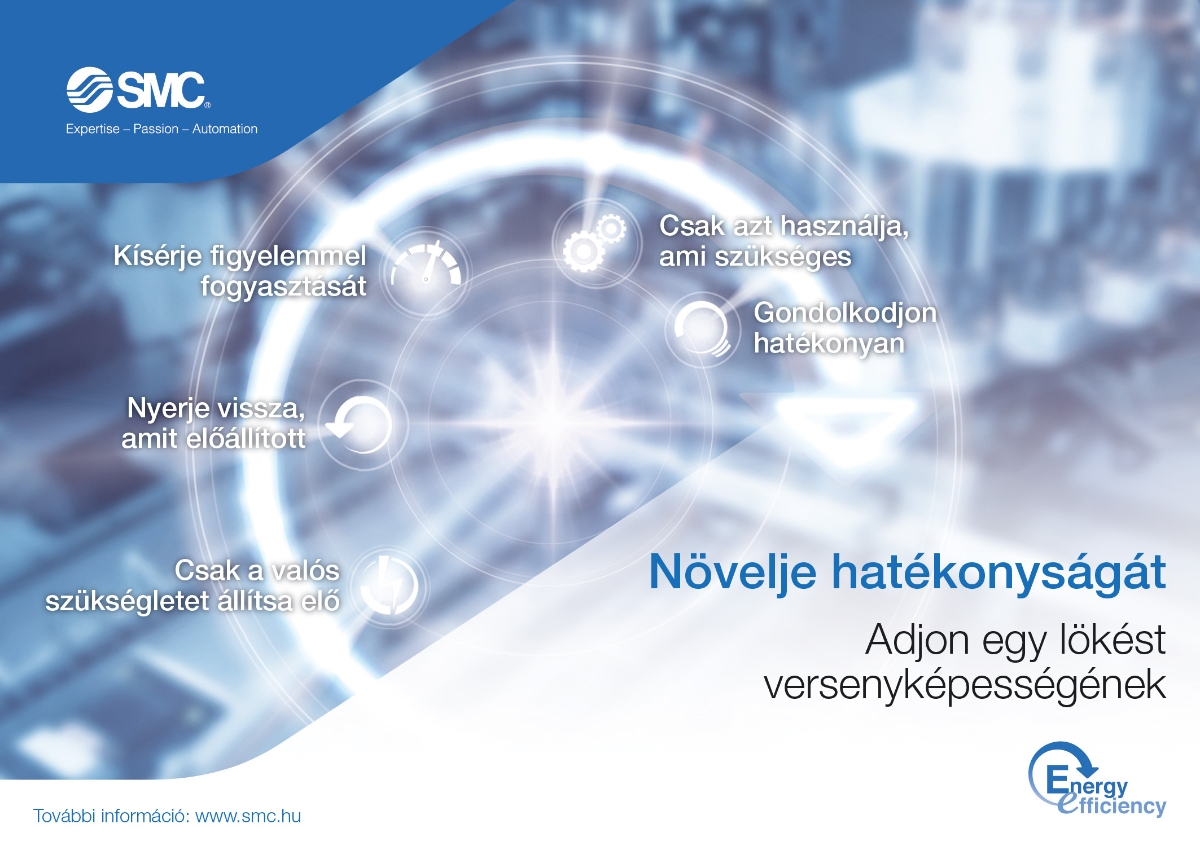
2019. dec. 1.