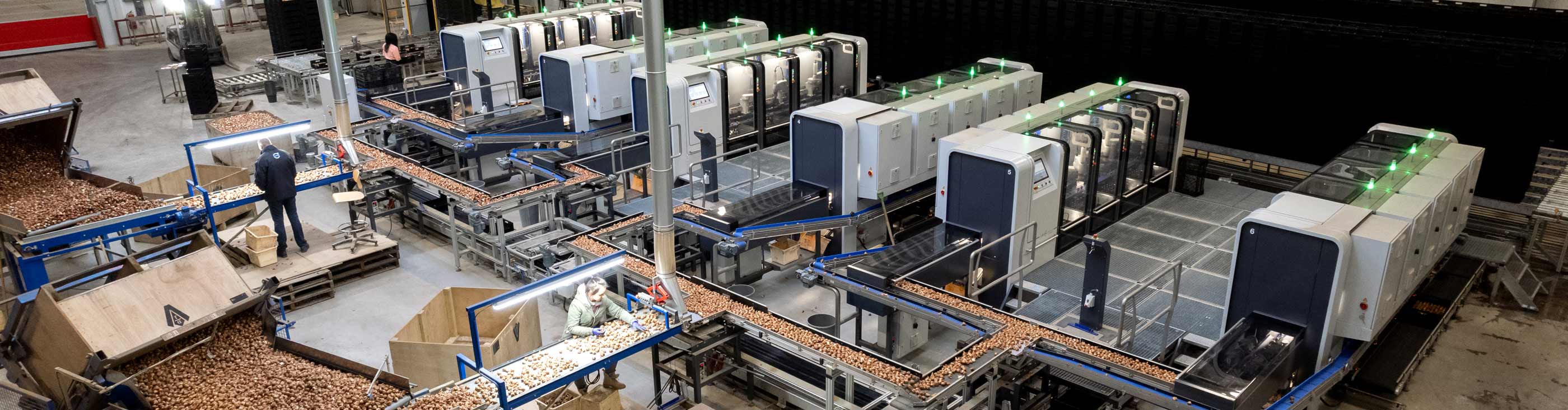
Automatizált folyamat a moduláris hagyma csomagoláshoz
Az ISO, Horti Innovators forradalmasítja a mezőgazdaság és a kertészet automatizálását a robotika, a látástechnológia, a mesterséges intelligencia és a gépi tanulás segítségével. A tulipánhagyma termesztők a kiemelt fókuszpontok közé tartoznak. Az ISO kifejlesztett egy vezeték nélküli kommunikációs megoldást, amelyet az SMC biztosított, ami lehetővé teszi a termesztők számára soha nem látott mennyiségű tulipánhagyma hatékony szortírozását és csomagolását, miközben összetett tervezési kihívásokat is megoldanak.
A tulipánhagymák csomagolása sokoldalú folyamat. Nagy mennyiségű hagymát kell kezelni, amelyeket meghatározott távolságban sorokba kell rendezni. Ezenkívül minden egyes hagymát úgy kell elhelyezni, hogy a hajtás (a tulipán szárának első jelei) felfelé nézzen. További nehézséget jelent, hogy a hagymák sértetlenek maradjanak a szállítás során, és a csomagoláson belüli helyes helyzetük megmaradjon. Ez elengedhetetlen, hogy elkerüljük a hajtások károsodását.
Az ISO kifejlesztett egy moduláris csomagolósort, amely automatizálja a teljes folyamatot. A legtöbb feladat elvégzésére robotokat és látástechnológiát használnak. „Ezek a gépek szabványosítottak, és az ügyfél igényei és elrendezése alapján testre szabhatók. Különböző típusú és méretű tulipánhagymákat tudnak feldolgozni vágott virágokhoz.” magyarázza Bastiaan Ophorst, az ISO gépészmérnöke.
Az intelligens csomagolás vezeték nélküli látórendszert igényel
A folyamat rövid ismertetése: egy targonca az előre kiválogatott tulipánhagymákat kocka alakú konténerekben szállítja, amelyeket a hagyma mérete szerint határoznak meg. A kocka alakú tárolókat a csomagolósor elején lévő gyűjtőtartályba ürítik, több réteg hagymát képezve. A rezgő asztalok segítségével a hagymákat egy töltőállomás felé szállítják ezzel biztosítva azt, hogy egy sorba rendeződjenek és megfelelő távolságot alakítsanak ki az egyes hagymák között a kívánt csomagolási mennyiség alapján.
Hat kamerát használnak a megfigyeléshez és minden egyes hagyma képének rögzítéséhez. A kombinált képeket 3D ábrázolás létrehozására használják, amely részletes információt nyújt a hagyma helyzetéről, 3D geometriájáról és a hajtás helyéről. Ezek az adatok elengedhetetlenek a robotkarokon lévő megfogók számára az egyes hagymák megfelelő kezeléséhez. Ezenkívül egy 3D kamera minden egyes hagymán optikai állapotellenőrzést végez, hogy megakadályozza az egészségtelen hagymák becsomagolását. Ezeket a hibás hagymákat, az úgynevezett „savanyú hagymákat” a csomagolósor irányító rendszere megjelöli, és eltávolítja a szalagról. A hagymák távolsága a szalag sebességének beállításával szabályozható, ezáltal megelőzve a folyamat során fellépő torlódásokat.
Miután a látórendszer meghatározza az hagymák helyzetét és irányát a szalagon, azok a kívánt távolságra kerülnek a csomagológépbe, tökéletes sort alkotva. A csomagolósor általában több modulból (úgynevezett „ültető egységekből”) áll, általában négy egységből, amelyek mindegyike egy-egy robottal van felszerelve. Az egyes hagymák helyzetéről és tájolásáról összegyűjtött információk alapján irányítja a megfogókat, hogy egy sor hagymát vegyenek fel és helyeznek el egy hídra. A hídon lévő pozíciók száma a csomagolótartály egyes soraiban elhelyezendő hagymák számától függ. A robotkar pontosan pozícionálja a hagymákat a hídon, biztosítva, hogy minden egyes hagymát biztonságosan tartson egy megfogó. Minden híd akár kétszer hét megfogó befogadására is alkalmas, két párhuzamos sorban, 180 fokban egymással szemben elhelyezve. Miután mind a hét megfogó megtelt, a híd elfordul, és a hagymasorok átkerülnek a csomagolóba. A hagyma típusától függően a csomagolás minden egyes pozíciója tartalmaz egy kis tűt a tulipánhagymák rögzítéséhez, vagy egy nedves talajréteget a hagymák stabilitása érdekében. A híd finoman rányomja a hagymákat a tűkre vagy a talajba, így rögzíti a helyzetüket. Ez garantálja, hogy a hagymák függőlegesen maradnak a termőterületre történő szállítás során. Miután a csomagolást megtöltötték, kicserélik üres csomagolásra. A hagymákkal megtöltött csomagolást ezután egy utolsó állomásra szállítják, ahol a termelő dolgozója szemrevételezéses ellenőrzést végez a szállítás előtt.
A hagymák elhelyezése a hídra
Megbízható vezeték nélküli kommunikáció
A vezeték nélküli kommunikáció létfontosságú szerepet játszott a csomagolósor tervezésénél felmerült technikai kihívás leküzdésében, kifejezetten a hidak forgó mozgása. Tekintettel arra, hogy a forgás mindig az óramutató járásával megegyező irányban történik, a vezetékes kommunikációs megoldások nem voltak praktikusak. Ophorst elmagyarázza: „Megvizsgáltuk a csúszógyűrűk használatának lehetőségét, de ezekhez nagyszámú vezetőre lett volna szükség. Mivel minden egyes plug-in hídban több mint harminc funkció/érzékelés van, a kábelezés nem volt kivitelezhető. Ekkor jöttünk rá, hogy a vezeték nélküli kommunikáció jelenti a továbblépést. De hogyan gondoskodhatunk a megbízhatóságról?”
„A megoldás az SMC-től jött” - mondja Bert Evertse, az ISO Horti csomagolósor vezérléséért felelős PLC programozója: „Korábban teszteltük egy másik márka Bluetooth-alapú termékét, de az interferenciára érzékenynek bizonyult, ami egy ilyen nagy sebességű alkalmazásnál nagyon nem kívánatos. Szerencsére az SMC a megfelelő megoldást kínálta a megfelelő időben. Egy ipari vezeték nélküli hálózatot javasoltak a csomagolósoron belül. A vonal nem forgó részéhez egy bázis (adó) modult, a csatlakozó hídhoz pedig egy távoli (vevő) modult telepítettünk. A plug-in híd vezérlési adatai az SMC ipari vezeték nélküli kommunikáción keresztül kerülnek továbbításra a bázisról a távvezérlőkhöz. A modulonként körülbelül 60 bitet tartalmazó vezérlési adatok, valamint a diagnosztikai információk Ethernet/IPTM-en keresztül jutnak el a bázisra. A bázis és a távvezérlők konfigurálása a telepítés során egyszer történik a Near Field Communication (NFC) segítségével.”
A bázis és a távvezérlők közötti távolság változhat, ebben a konfigurációban 5-6 méter. Maximálisan 10 méteres sugarú kör lehetséges. Meglepő módon az egyes modulokon belüli mozgó alkatrészek, például a robotkarok szervomotorjai nem befolyásolják az adatátvitelt. Evertse megerősíti: „Semmilyen meghibásodás nem történt. Valójában a kommunikáció rendkívül megbízható”.
Vezeték nélküli távvezérlő modul a plug-in hídon