Predictive maintenance has very much become an industry buzzword in recent decades as factories try to drive down their capital equipment TCO (total cost of ownership) by preventing failures and downtime in a ‘just-in-time’ way. Many wrongly assume that implementing a predictive maintenance strategy entails a complete overhaul of operations, but in reality, taking a few small steps can make a big difference to machine uptime and OEE (overall equipment effectiveness). To ensure success, it is advisable to engage with a trusted technology partner. For SMC, a global leader in pneumatic control solutions, the ‘P’ in predictive maintenance should stand for ‘progress’ not ‘pain’.
By Oliver Prang, Expert Digital Business Development, SMC Germany
DECEMBER 2021
According to an IndustryWeek report, unplanned downtime costs industrial manufacturers an estimated $50 billion annually. Equipment failure is behind 42% of this unplanned downtime. No one can therefore challenge the need for an effective maintenance regime.
Different strategies
There are many different types of maintenance, with reactive, preventative and predictive arguably the most common. But how is it possible to make sense of these seemingly disparate terms? Some suggest that using human health makes for a suitable analogy to machine health. Take diabetes, for instance, a disease currently affecting 422 million people globally, according to the World Health Organization.
Using reactive maintenance in this sense would be after a doctor has confirmed a patient’s diabetes. The patient will subsequently focus on taking injections or tablets to control blood glucose levels, alongside a controlled diet that reduces or even avoids the intake of sugar and carbohydrate. In complete contrast, applying preventative maintenance would be to treat the disease without any symptoms. The patient then continues to maintain a healthy lifestyle, supported by a controlled eating and exercise plan to hopefully avoid any risk of ever developing diabetes. Predictive maintenance is when someone is maybe ‘pre-diabetic’, but still within a safe limit or acceptable criteria. Regularly monitoring blood glucose and BMI (body mass index), for example, will reveal whether the situation is stable or deteriorating as time passes and help identify if/when more interventions are required.
Production engineers want to increase machine reliability by minimising the possibility of costly and disruptive downtime. In many cases this entails mixing various maintenance strategies in different production scenarios, rather than selecting the one that is trending on social media. There are many factors to consider here, not least the cost of implementation and management in comparison with the number of downtime instances.
Data is king
The key word is not even predictive or preventive, but data. Implementing a predictive maintenance programme requires three basic things: data, time and analysis. Data is an ally to get ahead of time - the modern version of a crystal ball - and increase machine reliability. Extensive knowledge is required of why an asset is beginning to fail. For precisely this reason, partnering with a reputable automation specialist can pay significant dividends.
From a practical perspective, rule number one is keep things simple. SMC supports customers with a ‘one-part-at-a-time’ approach, progressing from actuator leakage analysis, for example, through to partial machine analysis and whole machine analysis. Thus, all the knowledge, process definitions and personnel responsibilities transfer from a small project initially, to a bigger one in the smoothest possible way.
A good case in point is a pneumatic cylinder: the workhorse of many industrial machines. Among the common failure modes for pneumatic actuators is a leaking piston seal. These defects can be difficult to detect, leading to a loss of pressure. An operating pressure loss of just 0.1 MPa can negatively affect the theoretical force output of a cylinder (32 mm diameter piston) by 17%. A further side effect of a faulty gasket is an increase in air consumption in order to compensate for the leak.
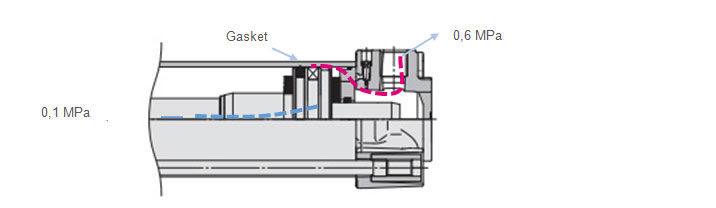
Theoretical output [N]

Chart Extraction from SMC´s CP96 catalogue
Here, adopting a predictive maintenance strategy entails little more than fitting a pressure sensor at each cylinder channel and monitoring pressure against time. Any defects in the gasket will soon become apparent due to abnormal performance curves in comparison with those ‘learned’ for normal operation. With machine learning and real-time analysis, it is possible to implement timely predictive maintenance before incurring any major performance losses or downtime.
As well as pressure sensors, other key sensors might include induction sensors to calculate cylinder speed and help detect levels of contamination on the guides, for example. Installing a network of flow sensors to continuously track the use of compressed air (and any leaks or malfunctions) over the pneumatic circuit is a further recommendation.
Real intelligence
Of course, not all intelligence is necessarily artificial. Sure enough, machines can learn, predict and prevent, but they still require human input to define suitable variables to monitor and set acceptable/unacceptable limits. In addition, humans must select which machine components to fit with sensors, as not all will be critical to uptime and productivity. Budgets, time and staff availability also come into the equation.
With these thoughts in mind, partnering with a proven technology specialist is a prudent strategy. For instance, pooling SMC’s knowledge of automation components with the individual machine knowledge of a customer makes for a powerful and resourceful combination.
Another potential factor here involves reliability-based maintenance. Designing from origin means identifying reductions in unnecessary maintenance costs based on FMEA (failure mode effects analysis). In essence, this approach focuses on the different failures that could occur and their potential consequences. SMC makes this task easy by hosting configurator tools on its website
For pneumatic airlines, valve manifolds and cylinders, helping to optimise product selection – and performance – for the application in hand.
Ultimately, many assume predictive maintenance is the be-all and end-all solution to reducing downtime and improving OEE. For now, this is not the case, although the situation could well evolve in coming years due to an increasing number of smart initiatives at factories around the world. Until then, bringing knowledge together is the key. As a team player, SMC is up for the challenge.