Even though almost all factories have air preparation systems to protect their pneumatic equipment, the subject is still not so well known, and it hides some interesting aspects and optimization. One of the key questions is how prepared should my compressed air be? There is not one simple answer to this question, because compressed air quality depends on a myriad of variables, such as the air quality coming in (from the compressor), the air quality requirements in the end-of-line applications, the process or industry requirements or even the position of the filtration units. With all these uncertainties, SMC, an Expert in air treatment, will be able to support you.
By Mark Brinsley, Sales Engineering Group; Air and Fluid Equipment, SMC UK
OCTOBER 2021
A prior triad to consider
Compressed air quality is just one of the 3 issues to consider:
- Dust and other airborne particles – The compressed air leaving the compressor room, which has already passed through a filter, still contains particles. If the air quality is too poor, it can ruin even the best actuators in just a few months, not to mention what it could do to sensitive end equipment such as flow sensors. The compressed air, if not treated, will contain varying levels of particles which will affect your production processes: the consequence will be generation of particle deposits leading to mechanical friction, e.g. between the cylinder wall and the piston seal.
- Water droplets or large potential for condensation – This ends up generating corrosion of parts and rust particles that can cause mechanical damage or block small flow cross sections. Moisture can also cause seals to swell resulting in additional friction in actuators. Other issues that might occur are:
- spray painting by change in color, adherence and finish quality
- industrial ink-jet printers in adherence and finish quality
- blow molding plastic bottles’ viscosity and material consistency
- gluing/taping adhesiveness of cardboard boxes
- pharmaceuticals compound mixing and integrity
- food processing contamination because of micro-organism growth
- air purge or air cooling where moisture will cause problems
- Oil mist carryover or odour from a compressor: consequences are particle clumping leading to blocked cross sections. Additionally, oil can cause some elastomers such as those in the seals to swell up.
In summary, inadequate air preparation causes higher maintenance costs, operating malfunctions, reduces service life and creates higher energy costs due to leakages. The kind of issues all of us want to avoid.
Optimized filtration system – The players involved to remove impurities in your compressed air
Depending on the impurities you need to remove, you will need to install different elements. When we talk about air preparation, we tend to think it just refers to filters, but having an optimized filtration system goes beyond that.
Air preparation is not just about filters. It should be considered as a whole system:
- Filters to remove the dust and particles are included in the Air Combination unit made of an air filter, a mist separator, a micro mist separator and an odour removal filter. SMC offers a complete range with a uniform design: air preparation equipment to meet the highest levels of air quality through multistage filtration from basic particle removal (AF series), mist separators (AFM / AFD), activated carbon filters (AMK) to bacterial removal (SFDA). Regulation of the supply pressure is carried out by regulators or filter / regulators. They provide a controlled set pressure with precision regulators being able to hold a set pressure with a reduced impact from flow rates and supply pressure influence. Without local regulation, the supply air pressure from the compressor could be considered wasteful in terms of energy efficiency, as well as potentially dangerous by allowing higher forces from actuators. There may also be plenty of situations where the higher pressure is too much for the local pneumatic equipment. To improve moisture removal a membrane filter can be added to the FRL unit. It might be considered in circumstances where factory piping is exposed to ambient temperatures lower than the dew point achievable by refrigerated drying.
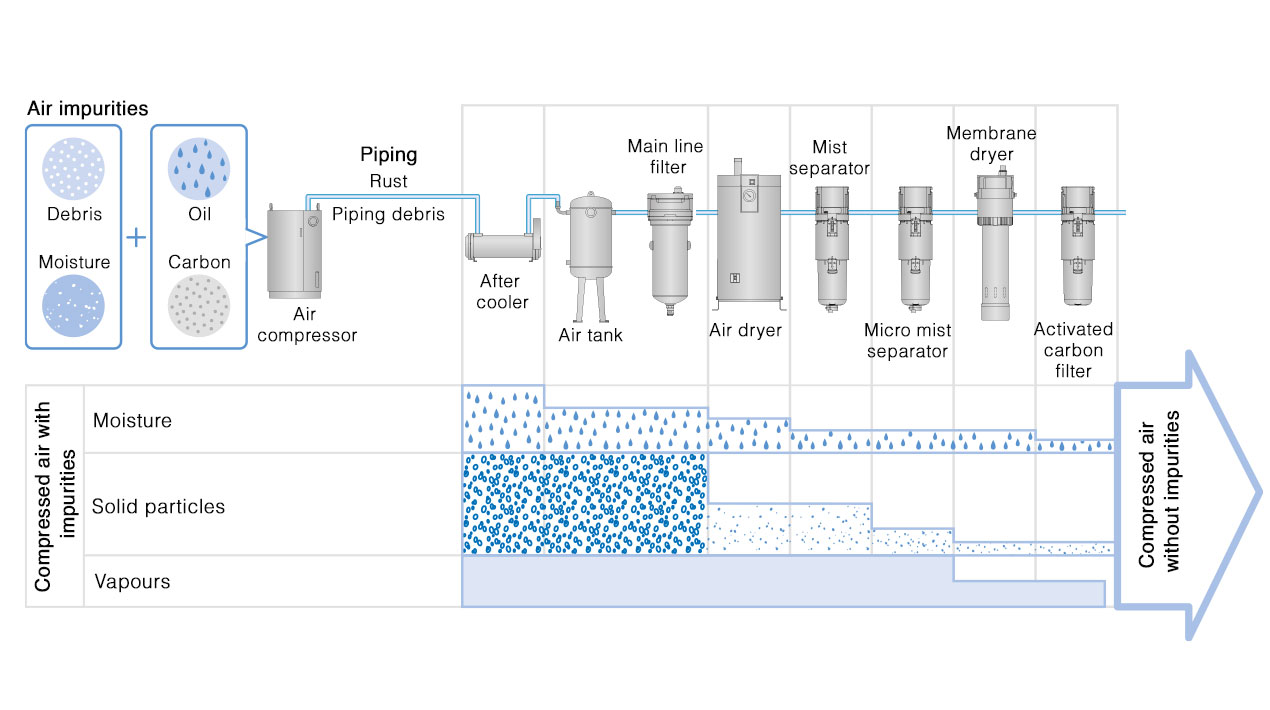
- Additionally, other components which help to control the operation:
- Electronic proportional regulators (allowing signalled controlled set pressures useful for stand by pressure reduction)
- Air flow switches with integrated temperature sensing (to establish “normal” consumption rates and to trigger the sensor if those conditions change for example, in the event of a leak developing.
- Monitored air dump valves (for safety circuits)
- Integrated pressure detection (checking if pressures are too high or low) or Slow pressure build up control (to prevent problems of sudden actuator start up)
Once your compressed air supply is adequately conditioned - and it should be monitored - your equipment will be safeguarded. Condition monitoring can also make it easy to plan routine maintenance to ensure efficient operation. Pressure switch and flow sensors will help to identify when maintenance should be carried out on a filter, such as emptying dust collectors.
- Refrigerated air dryers to remove moisture. They should be protected by a main line filter. A refrigerated dryer will further cool the compressed air by removing heat at its inlet side and lowering its temperature dew point down to 3ºC, then expelling the condensation through an automatic condensation drain. The dryer will then reheat the dried compressed air back to ambient temperature by recycling the previously removed heat using a heat exchange process. This reheating of the compressed air to an ambient temperature will eliminate “sweating” on cold pipes when working in humid factory conditions.
Additionally, water separators are an important option. They use mechanical separation techniques to remove condensed water in bulk from factory air either by directing inlet air into a spiral and using centrifugal force to separate the water out from the compressed air, or by passing the inlet air through a special resin filter with large meshes to trap water particles that will then drop down to a collection bowl, allowing the compressed air to pass through. SMC’s new AFF series of water separator that combine water removal AND filtration of particles IN A SINGLE FILTER, is capable of removing water droplets up to a 99% water removal rate, using a special resin filter to trap water droplets.
However, a water separator is designed to remove water, but it doesn’t lower the dew point which is usually done by a refrigerated air dryer. If it is not enough, you may use a membrane filter to reduce the dew point at the point of use.
Do not over specify
Assessing the acceptable level of dust, moistness and other potential contaminants will be defined according to the application and the numerous issues that may occur. For sensitive equipment, the ISO standard 8375-1 will help to define the suitable numeric grading for particles and oil content. In simple terms, the lower the number for each category, the cleaner the compressed air.
Air preparation equipment has improved over the last few decades, minimizing the flow loss in the circuit thanks to optimization of the internal valve construction. However, Compressed air quantity (Flow) needs to be considered to ensure you can meet the flow requirements of your equipment. This means that the components in the compressed air circuit must be suitably sized based on your flow requirements. Too small and it would be inefficient and you would see a larger drop in pressure, too big and it would be a waste of money.
Clearly, compressed air pressure should be considered when selecting your model, ensuring all components operate for your required pressure in the system. Optimised operating pressure increases efficiency; efficiency is increased by running equipment at lower pressures, thus reducing the amount of compressed air lost in leaks. If you lower the operating pressure of your equipment then you could also reduce demand from the compressor and save power consumption.
It is vital to consider pressure and flow when properly sizing filtration components in your search for an efficient air quality solution. It is very important NOT TO OVER SPECIFY the cleanliness of compressed air. Unnecessarily over filtering can increase potential pressure drops, can make a compressed air system less efficient and can lead to exorbitant energy bills.
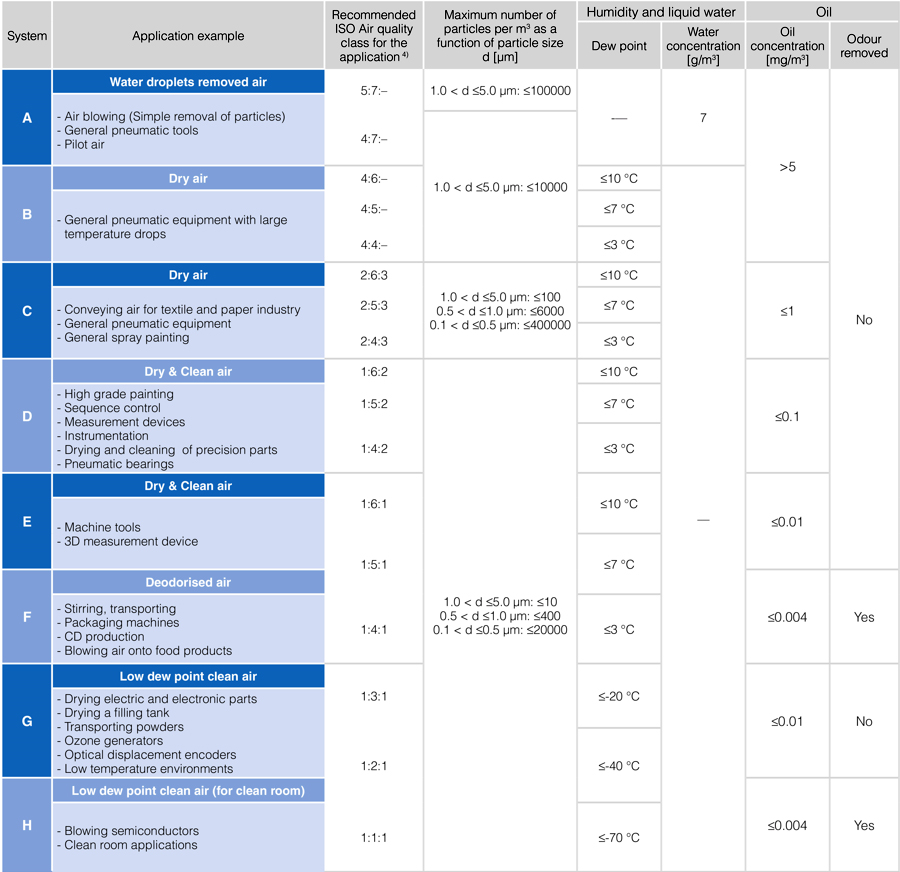
A vital final step – cartridge cleansing>
Why do you normally empty your vacuum cleaner every now and then? Because it loses power. The same happens with your filtration units. When the cartridge is full performance is reduced, generating pressure drops; significant pressure drops result in poor machine functioning which in many cases leads to turning up the regulator. So, cleaning the cartridge, in the same way we clean our vacuum cleaner every now and then is simpler than turning up the pressure, which can be costly and inefficient.
To conclude, it is a fact that the air let out by the compressor contains impurities. If the air is not treated according to the necessities of your process, those impurities will end up contaminating the final output. Different applications require different level of filtration and overall air treatment. Count on SMC Experts to find the best air treatment for your compressed air system.