Anche se quasi tutte le fabbriche dispongono di sistemi di trattamento dell'aria per proteggere le apparecchiature pneumatiche, l'argomento non è ancora così conosciuto e nasconde alcuni aspetti interessanti di ottimizzazione. Una delle domande chiave è: quanto deve essere trattata l'aria compressa? Non c'è una risposta semplice a questa domanda, perché la qualità dell'aria compressa dipende da una miriade di variabili, come la qualità dell'aria in ingresso (dal compressore), i requisiti di qualità dell'aria nelle applicazioni di fine linea, il processo o requisiti del settore o anche la posizione delle unità di filtrazione. Con tutte queste incertezze, SMC, esperta nel trattamento dell'aria, sarà in grado di assistervi.
di Mark Brinsley, Sales Engineering Group; Air and Fluid Equipment, SMC UK
OTTOBRE 2021
Tre cose da valutare in anticipo
La qualità dell'aria compressa è solo una delle 3 questioni da considerare:
- Polvere e altre particelle trasportate dall'aria – L'aria compressa che lascia la stanza del compressore, che è già passata attraverso un filtro, contiene ancora particelle. Se la qualità dell'aria è troppo scarsa, può rovinare anche i migliori attuatori in pochi mesi, per non parlare di ciò che potrebbe fare alle apparecchiature finali sensibili come i sensori di flusso. L'aria compressa, se non trattata, conterrà livelli variabili di particelle che influenzeranno i vostri processi di produzione: la conseguenza sarà la generazione di depositi di particelle che portano all'attrito meccanico, ad esempio tra la parete del cilindro e la guarnizione del pistone.
- Gocce d'acqua o condensazione - Questo finisce per generare corrosione delle parti e particelle di ruggine che possono causare danni meccanici o bloccare piccole sezioni di flusso. L'umidità può anche causare il rigonfiamento delle guarnizioni con conseguente attrito aggiuntivo negli attuatori. Altri problemi che potrebbero verificarsi sono:
- verniciatura a spruzzo per cambiamento di colore, aderenza e qualità della finitura
- stampanti industriali a getto d'inchiostro in aderenza e qualità di finitura
- viscosità e consistenza del materiale delle bottiglie di plastica per soffiaggio
- incollaggio/sigillatura di scatole di cartone
- miscelazione e integrità dei composti farmaceutici
- contaminazione da lavorazione degli alimenti a causa della crescita di microrganismi
- spurgo o raffreddamento dell'aria dove l'umidità causerà problemi
- Nebbia d'olio di trascinamento o odore da un compressore - Le conseguenze sono il raggruppamento delle particelle che porta a sezioni trasversali bloccate. Inoltre, l'olio può far gonfiare alcuni elastomeri come quelli delle guarnizioni.
In sintesi, una preparazione inadeguata dell'aria causa maggiori costi di manutenzione, malfunzionamenti operativi, riduce la durata di vita e crea costi energetici più elevati a causa delle perdite. Il tipo di problemi che tutti noi vogliamo evitare.
Sistema di filtraggio ottimizzato: gli attori coivolti per rimuovere le impurità nella vostra aria compressa
A seconda delle impurità da rimuovere, è necessario installare diversi elementi. Quando si parla di preparazione dell'aria, si tende a pensare che ci si riferisca solo ai filtri, ma avere un sistema di filtraggio ottimizzato è qualcosa di più.
La preparazione dell'aria non riguarda solo i filtri. Dovrebbe essere considerata come un intero sistema:
- I filtri per rimuovere la polvere e le particelle sono inclusi nell'unità Air Combination composta da un filtro dell'aria, un separatore di nebbia, un separatore di micro nebbia e un filtro di rimozione degli odori. SMC offre una gamma completa con un design uniforme: apparecchiature di preparazione dell'aria per soddisfare i più alti livelli di qualità dell'aria attraverso la filtrazione multi-stadio dalla rimozione delle particelle di base (serie AF), ai separatori di nebbia (AFM/AFD), ai filtri a carbone attivo (AMK), alla rimozione batterica (SFDA). La regolazione della pressione di alimentazione è effettuata da regolatori o filtri/regolatori. Essi forniscono una pressione impostata controllata con regolatori di precisione in grado di mantenere una pressione impostata con un impatto ridotto dalle portate e dall'influenza della pressione di alimentazione. Senza una regolamentazione locale, la pressione dell'aria di alimentazione dal compressore potrebbe essere considerata uno spreco in termini di efficienza energetica, oltre che potenzialmente pericolosa, consentendo forze più elevate dagli attuatori. Ci potrebbero anche essere molte situazioni in cui la pressione più alta è eccessiva per l'attrezzatura pneumatica locale. Per migliorare la rimozione dell'umidità, all’unità FRL può essere aggiunto un filtro a membrana. Potrebbe essere considerato in circostanze in cui le tubature della fabbrica sono esposte a temperature ambientali inferiori al punto di rugiada raggiungibile con l'essiccazione refrigerata.
- Inoltre, altri componenti che aiutano a controllare il funzionamento:
- Regolatori elettronici proporzionali (che permettono di controllare le pressioni impostate, utili per la riduzione della pressione in stand-by)
- Flussostati dell'aria con rilevamento della temperatura integrato (per stabilire i tassi di consumo “normali” e per far scattare il sensore se queste condizioni cambiano, per esempio, in caso di sviluppo di una perdita.
- Valvole di scarico dell'aria monitorate (per i circuiti di sicurezza)
- Rilevamento integrato della pressione (controlla se le pressioni sono troppo alte o basse) o controllo dell'accumulo lento di pressione (per prevenire problemi di avvio improvviso dell'attuatore).
Una volta che la vostra fornitura di aria compressa è adeguatamente condizionata - e dovrebbe essere monitorata - la vostra attrezzatura sarà salvaguardata. Il monitoraggio delle condizioni può anche facilitare la pianificazione della manutenzione ordinaria per assicurare un funzionamento efficiente. I sensori di pressione e di flusso aiuteranno a identificare quando la manutenzione deve essere effettuata su un filtro, come lo svuotamento dei collettori di polvere.
- Essiccatori ad aria refrigerata per rimuovere l'umidità. Dovrebbero essere protetti da un filtro della linea principale. Un essiccatore refrigerato raffredda ulteriormente l'aria compressa rimuovendo il calore al suo ingresso e abbassando il suo punto di rugiada fino a 3ºC, poi espellendo la condensa attraverso uno scarico automatico della condensa. L'essiccatore riscalderà poi l'aria compressa essiccata di nuovo a temperatura ambiente riciclando il calore precedentemente rimosso attraverso un processo di scambio di calore. Questo riscaldamento dell'aria compressa a una temperatura ambiente eliminerà la “sudorazione” sui tubi freddi quando si lavora in condizioni di fabbrica umide.
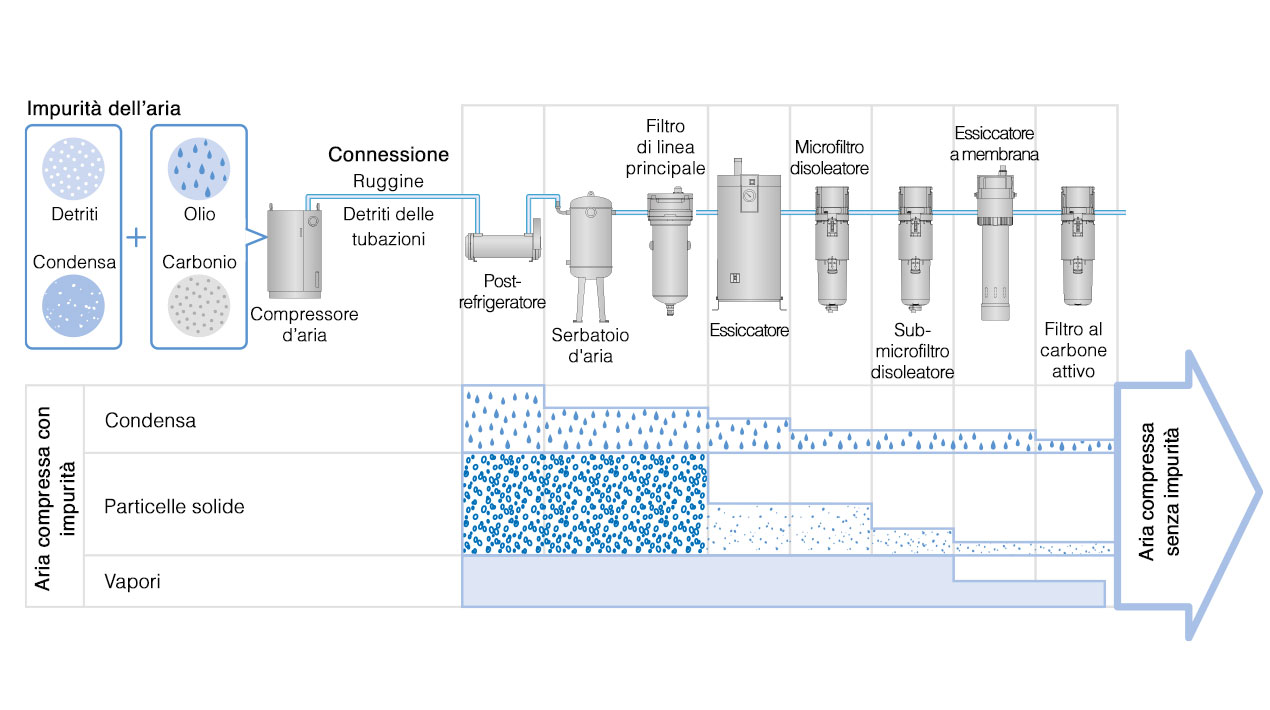
Anche i separatori d'acqua sono un'opzione importante. Usano tecniche di separazione meccanica per rimuovere l'acqua condensata alla rinfusa dall'aria di fabbrica o dirigendo l'aria in entrata in una spirale e usando la forza centrifuga per separare l'acqua dall'aria compressa, o facendo passare l'aria in entrata attraverso un filtro di resina speciale con grandi maglie per intrappolare le particelle d'acqua che poi scenderanno in una ciotola di raccolta, lasciando passare l'aria compressa. La nuova serie AFF di SMC di separatori d'acqua che combinano la rimozione dell'acqua e la filtrazione delle particelle in un unico filtro, è in grado di rimuovere le gocce d'acqua fino a un tasso di rimozione del 99%, utilizzando un filtro di resina speciale per intrappolare le gocce d'acqua.
Un separatore d'acqua è progettato per rimuovere l'acqua, ma non abbassa il punto di rugiada, abbassamento che è prodotto da un essiccatore d'aria refrigerata. Se non è sufficiente, potrete usare un filtro a membrana per ridurre il punto di rugiada nel punto di utilizzo.
Non esagerare troppo
La valutazione del livello accettabile di polvere, umidità e altri potenziali contaminanti sarà definita in base all'applicazione e ai numerosi problemi che potranno verificarsi. Per le attrezzature sensibili, la norma ISO 8375-1 aiuterà a definire la classificazione numerica adatta per le particelle e il contenuto di olio. In parole semplici, più basso è il numero per ogni categoria, più pulita è l'aria compressa.
Le attrezzature per la preparazione dell'aria sono migliorate negli ultimi decenni, minimizzando la perdita di flusso nel circuito grazie all'ottimizzazione della costruzione della valvola interna. Tuttavia, per assicurarsi di poter soddisfare i requisiti di flusso della vostra attrezzatura, deve essere considerata la quantità di aria compressa (flusso). Ciò significa che i componenti del circuito dell'aria compressa devono essere adeguatamente dimensionati in base alle vostre esigenze di flusso. Troppo piccolo sarebbe inefficiente e osservereste un maggiore calo di pressione, troppo grande e sarebbe uno spreco di denaro.
Chiaramente, quando si sceglie il modello deve essere considerata la pressione dell'aria compressa, assicurando che tutti i componenti funzionino per la pressione richiesta nel sistema. Una pressione operativa ottimizzata aumenta l'efficienza; l'efficienza viene aumentata facendo funzionare le attrezzature a pressioni più basse, riducendo così la quantità di aria compressa persa in perdite. Se abbassate la pressione d'esercizio della vostra attrezzatura, potreste anche ridurre la domanda del compressore e risparmiare sul consumo di energia.
Quando si dimensionano correttamente i componenti di filtrazione nella ricerca di una soluzione efficiente per la qualità dell'aria, è vitale considerare la pressione e il flusso. È molto importante non esagerare troppo con la pulizia dell'aria compressa. Un filtraggio eccessivo non necessario può aumentare le potenziali cadute di pressione, può rendere un sistema d'aria compressa meno efficiente e può portare a bollette energetiche esorbitanti.
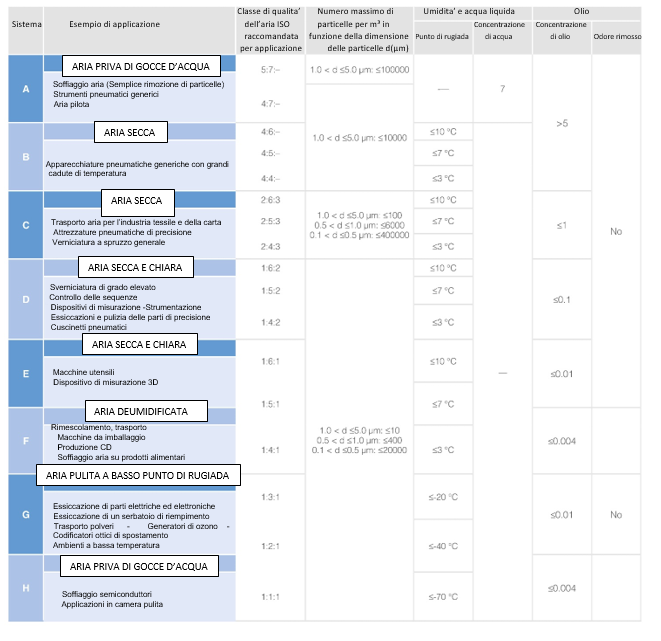
Un ultimo passo vitale: la pulizia della cartuccia
Perché normalmente ogni tanto svuotate l'aspirapolvere? Perché perde potenza. Lo stesso accade con le vostre unità di filtraggio. Quando la cartuccia è piena, le prestazioni si riducono, generando cali di pressione; cali di pressione significativi si traducono in un cattivo funzionamento della macchina che in molti casi porta ad alzare il regolatore. Quindi, pulire la cartuccia, nello stesso modo in cui puliamo il nostro aspirapolvere ogni tanto, è più semplice che alzare la pressione, cosa che può essere costosa e inefficiente.
Per concludere, che l'aria rilasciata dal compressore contenga impurità è un fatto. Se l'aria non è trattata secondo le necessità del vostro processo, queste impurità finiranno per contaminare l'output finale. Applicazioni diverse richiedono un diverso livello di filtrazione e di trattamento generale dell'aria. Contate pure sugli esperti SMC per trovare il miglior trattamento dell'aria per il vostro sistema di aria compressa.