The trend is clear, and there is no going back. Consumer environmental and sustainability concerns, in terms of plastic pollution and the rise of Circular Economy principles consciousness compel the packaging industry towards a more ethical packaging. This means using material easier to recycle like monolayer plastic or paper and reducing the quantity of material used. Moving towards sustainable packaging brings technical challenges to packaging machines. Furthermore, ensuring higher sustainability goes through higher efficiency. How? Keep on reading.
By Jorge Salgado, Food & Packaging Industry Manager, SMC Spain
AUGUST 2021
By 2030 all plastic packaging within the EU will need to be recyclable or reusable. It will concern all kinds of packaging, for primary to secondary packaging, where paper-based materials are often utilized: plastic bottle blow moulding, rigid tray hot stamping, sealing with films or all kinds of bags with flexible material.
Less material or new material, the problem is the same. Processes must be more accurate, better controlled, and easy to set-up.
Multi-layer plastic in the spotlight as the main way to address plastic pollution
Conventional multi-layer composite films are complex and expensive to recycle because of the need to separate the different film layers. Polymer-based multilayer packaging materials are commonly used in order to combine the respective performance of different polymers, the advantages that they bring to packaging are numerous. However, because of their poor recyclability, most multilayers are usually incinerated or landfilled, counteracting the efforts towards a circular economy. Additionally, many countries do not have the necessary recycling systems and processes in place to recycle complex laminates. By contrast, monomaterial films are fully recyclable as all layers are made of the same type of plastic.
Concerning the manufacturing process, the transition from multilayer to monomaterial involves some changes. Today, operators have to manually adjust their process and to do some tests before launching the full batch. It must be mentioned that operators need a real know-how as there is no modelling tool enabling to set parameters (time, temperature, pressure…) according to the material property. Process modelling might even be impossible as materials will change from one batch to another. After all the objective is to recycle and re-use plastic, but composition changes as we mix different sources, sometimes directly on the factory floor, and because the more a plastic is recycled the more it will break its carbon chain and material properties. These settings are complex and time consuming and they may change from one batch to another according to the material, even for very similar productions!
Another specific problem with monomaterials to consider is the required sealing technology, especially in high-speed range. Operators need to adjust parameters like sealing time, temperature or pressure. For a film, heat sealing has to be aligned precisely to prevent damage to the heat-sensitive outer layer while ensuring the sealing integrity of the inner layer.
What about paper-based solutions?
Another superior sustainable alternative are the paper-based solutions. The higher eco-friendliness of this alternative lays mainly in the end-of-life perspective. Once in the environment, paper-based packaging can break down within months, but plastics can take decades or even centuries to degrade. Much of this finds its way into the sea. According to the European Environment Agency, 82% of the litter collected on European beaches is plastic, while only 2% is paper or cardboard Furthermore, the paper recycling rate across Europe already at about 80%.
In term of process, sealing is of course also a challenge as it involves accurate adhesion technologies. The biggest problem might be however the cardboard particles which may generate failures and loss of performances.
Less plastic altogether
The third trend in sustainable packaging involves packaging redesigning to reduce the quantity of material. Here manufacturing tolerances are smaller and precision, repeatability are essential.
Summarizing, this switch to sustainable packaging will involve better precision and better control of the processes to anticipate problems. It will also require a speed-up in production changes. Moreover, meeting ethical packaging objectives, could end up generating an extra-cost of 30 or 40%. This is our proposal to counteract this challenge.
Think about OEE!
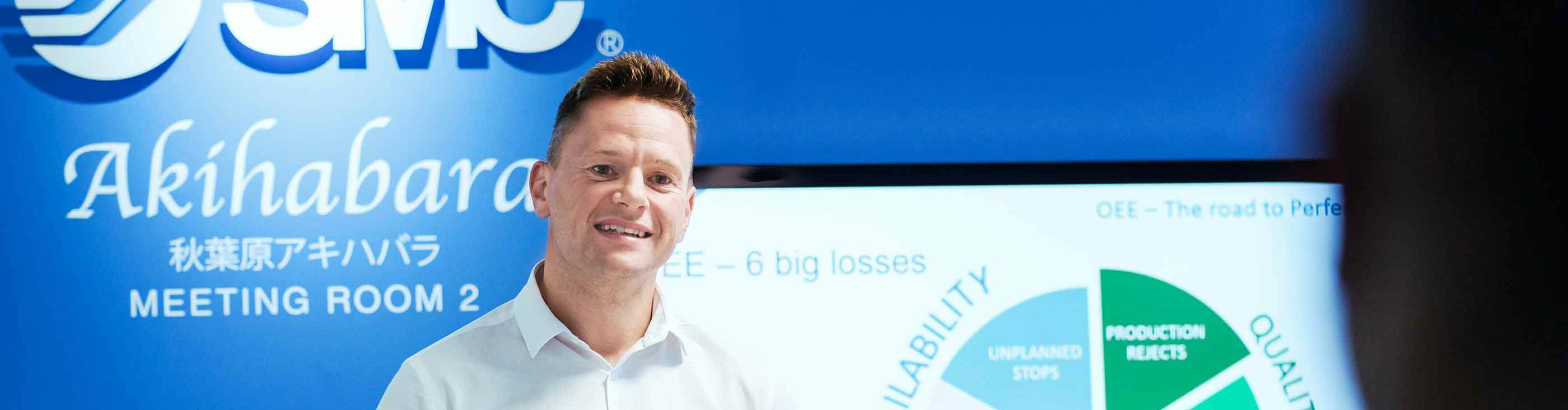
Overall Equipment Effectiveness (OEE) is a very practical way to prepare and mitigate the challenges of the next decade. Manufacturing only good parts (quality), as fast as possible (performance) with no stop time (availability).
Sustainable packaging will for sure put OEE on the ropes. It will increase all these production losses, as setting times are longer and product quality is harder to maintain. This issue will affect machine-builders, but also end-users who are often upgrading or revamping their machinery, instead of investing in a new production line.
For example, if the sustainable packaging alternative is paper-based, this encloses pollution and related risk of failure, compromising product quality. For instance, it requires the installation of cylinders with lube retainer in order to maintain a grease film on the piston rod surface and to prevent entry of dust or other pollutants. These cylinders improve by 4 the number of operating cycles. We propose the use of vacuum systems with integrated in-line air filters and lock mechanism or transparent bowls. Furthermore, an adequate selection of the vacuum pad material can reduce line stops. A last alternative to ensure quality in paper dust environment is to switch to the cyclonic vacuum technology where a positive pressure is supplied to the ejector side of vacuum end-effector to eject powder.
However, there are other non-sustainable-related-packing issues, associated with product quality that if addressed can increase OEE, and assist in alleviating the extra cost and hassle that the eco alternatives bring to the manufacturing process.
Addressing overall product quality – some examples
- Start-up rejects
Plastic wrap, foam packing, or labels cling and attract dust and dirt, causing misapplication or contamination to pharmaceutical and food packaging. Industrial ionizers are the primary tools for static elimination, neutralization, and control. They are available in bar, nozzle and fan types to better accommodate a variety of production spaces that have accumulated static electricity problematic to manufacturing processes.
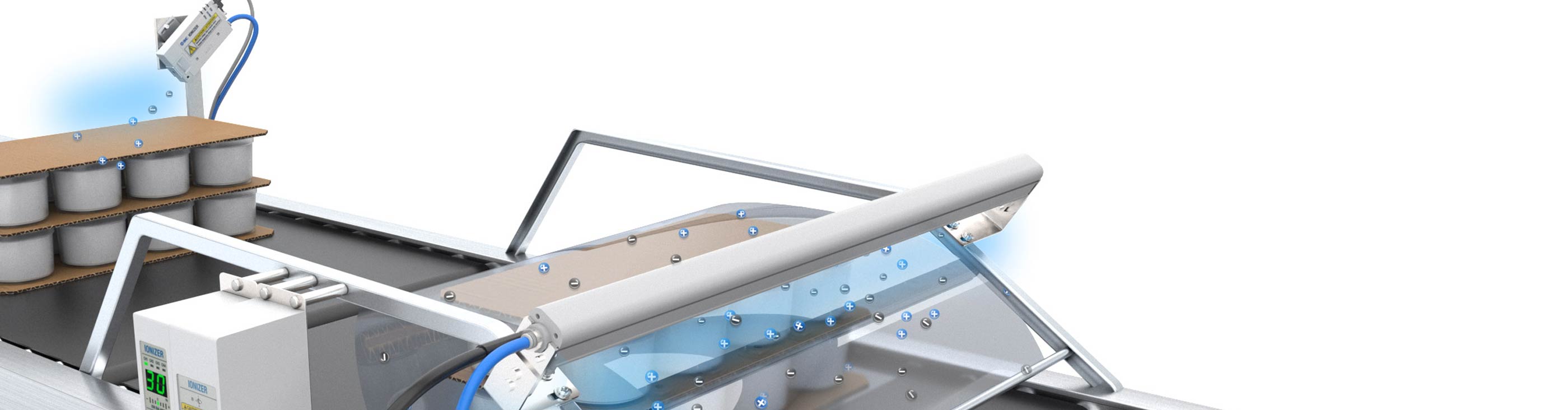
- Production rejects
For plastic bottle blowing and sealing, temperature control is one of the key parameters enabling to maintain quality and to ease set-up time. SMC will provide with a full range of solutions to handle this when it is about cooling the plastic or the sealing after production. They can be controlled digitally.
Increase performance with digital control
The star solution for addressing performance are digital sensors and connected devices. We rely on a wide portfolio to digitalize all components, to ease production change over, reduce set-up time and that allow configurations to be saved. Sensors and switches that help to implement effective predictive maintenance and check the whole system performance in real time.
Every detail counts to reduce downtimes and maintain operating parameters and thus precision and quality
- High quality sealing.
- Flow or pressure switch enabling real time monitoring to avoid unplanned maintenance and to guarantee actuators performance.
- Actuators with metal sealing featuring less wear offering maintenance free operations and stable performance.
- Tubing can be improved with a CAD tool to minimize cable length and associated losses in pressure and precision. Additionally, colour tubing will ease installation and maintenance while reducing potential errors.
- Before the marking, rotary units can be used for a perfect positioning and blow amplifiers to prepare the surface, offering great return on investment.
- Standard magnetic switches which can be adapted to any of our actuators.
- Speed controller, maintenance or settings can be done in a much faster way: forget about the screw to adjust the flow and use its user-friendly wheel for a clear display of the value.
- Valves, SMC also provides valve systems which allows one valve to change without interrupting the operation of the valve island (hot swap).
- On the top of this, practical training will enable operators to quickly solve simple problems.
Plastic pollution is an issue to be addressed by all members of society. As consumers and as manufacturers we are sustainably conscious. However, this is going to involve many manufacturing challenges in the next 5 to 10 years. These challenges materialize in machine modifications, higher costs and production uncertainties, which as discussed, can be eased by addressing OEE. At SMC we rely on local packaging trained teams ready to support our customers in the transition to sustainable packaging.